This blog post defines stress and strain, explains the difference between normal and shear stresses, and introduces the concept of von Mises stress, which is crucial for understanding metal plasticity.
Normal Stresses and Strains
Stress is a measure of the local concentration of mechanical force. Consider a body subjected to equal and opposite forces on two faces (Fig.1). If these forces act perpendicular to a face (ie parallel to its face normal), as shown, the stress σ (sigma) is termed a normal stress. This may be tensile (positive) or compressive (negative).
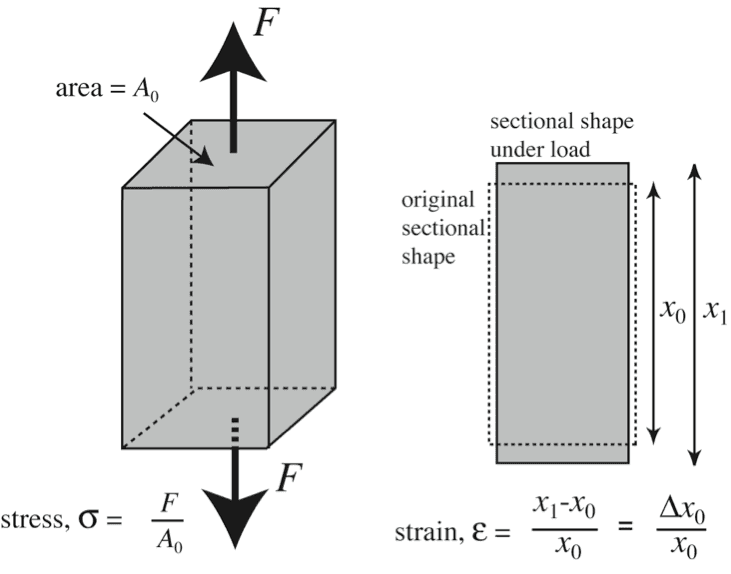
The area being loaded will reduce as F increases and the material progressively deforms. Therefore, at relatively large strains, the stress defined as F/A0, termed the nominal stress or the engineering stress, differs significantly from the true stress (defined as the force divided by the current area).
The response of the material to the applied stress is characterised by the strain. The normal strain in a particular direction, usually termed ε (epsilon), is the change in length along that direction, divided by the original length. In the same way as for stresses, a distinction can be drawn between this nominal or engineering strain and the true strain (defined as the change in length divided by the current length).
Shear Stresses and Strains
It’s also possible to apply forces parallel to two opposite faces of a body, so as to generate shear. Shear forces must be applied in pairs, if the body is not to rotate. This is illustrated in Fig. 2.
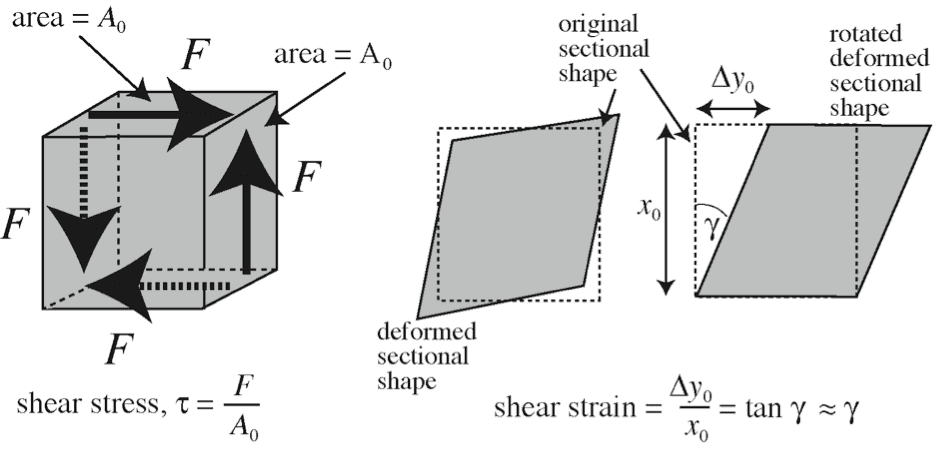
Stresses and Strains as Second Rank Tensors
A stress, or a strain, therefore has two directions associated with it – the direction of the applied force (i) and the direction of the normal of the plane on which the force acts (j). The values of i and j can be 1, 2 or 3 (the three orthogonal reference directions). A stress should thus be expressed as σij, which is a tensor of second rank. (A scalar is a tensor of zeroth rank, with no subscript, while a vector is a tensor of first rank, with one subscript.) The stress σij is a normal stress if i = j and a shear stress otherwise. A general stress state (and a strain state) should therefore be expressed as an array of 9 numbers, although this is reduced to 6 when it is recognised that, in order to avoid rotation, σij = σji (ie the tensor is symmetric). Furthermore, a general state of stress can always be represented just by three principal stresses, σ1, σ2 and σ3, which are normal stresses acting in three orthogonal directions (the principal directions).
Deviatoric (von Mises) and Hydrostatic Stresses and Strains
While the loading configurations described above are simple, with just a single stress being generated in the sample, more complex (multi-axial) stress states are common. Plastic deformation of metals is stimulated solely by the deviatoric (shape-changing) component of the stress state, often termed the von Mises stress, and is unaffected by the hydrostatic (volume-changing) component. This is follows from the fact that plastic deformation (of metals) occurs at constant volume. One consequence of this is that the material response (stress-strain relationship) is the same in tension and compression (provided that true stresses and strains are being used).
The von Mises stress, which is a scalar quantity, is related to the principal stresses by:
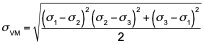
The hydrostatic stress, which is also a scalar, can be written:

Under simple uniaxial tension or compression, the von Mises stress is equal to the applied stress, while the hydrostatic stress is equal to one third of it. The von Mises stress is always positive, while the hydrostatic stress can be positive or negative. It is not appropriate to think of the von Mises stress as being “tensile”, as one would if it were a normal stress (with a positive sign). It’s effectively a type of (volume-averaged) shear stress. Shear stresses do not really have a sign, but it’s conventional to treat them as positive, as indeed is done for the von Mises stress.
It’s also possible to identify deviatoric and hydrostatic components of the (plastic) strain state. Analogous equations to those above are used to obtain these values. The von Mises strain is often termed the “equivalent plastic strain”. Again, it always has a positive sign, but this does not mean that it is a “tensile” strain. The hydrostatic plastic strain, on the other hand, always has a value of zero. This follows from the fact that plastic strain does not involve a change in volume. (This is not true of elastic strains, which do in general involve a volume change.)
Many loading situations create complex stress fields that are not only multi-axial, but also vary with position in the component (sample). These situations can be modelled using the Finite Element Method (FEM), in which the component is divided up into a large number of separate volume elements, with the stress-strain relationship concerning being satisfied in all of them. This can be done using a simple (uniaxial) relationship, provided the von Mises stress and the von Mises strain are used in it.