Innovation in advanced manufacturing is transforming the way in which we produce products across a range of industrial settings. But in order to achieve this potential, researchers need fast, reliable strategies for material characterisation, process optimisation, and quality control.
Research teams at The Cote Research Lab at Worcester Polytechnic Institute (WPI) are pushing the boundaries in materials characterisation for large-scale metal additive manufacturing (AM) processes, including cold spray deposition and wire-arc DED. Their model-guided approach to materials development supports a wide range of applications across the aerospace, naval, and energy industries.
To meet the demands of fast-paced research and applied testing, the team relies on the full suite of Plastometrex technology. These tools utilise Profilometry-based Indentation Plastometry (PIP) to enable high-throughput testing that supports rapid characterisation and materials development. By leveraging the full suite of PIP testing technology, from initial R&D through to final part qualification, the team at the Cote Research Lab has dramatically streamlined their workflows, ensuring new materials and processing techniques are rapidly adopted.
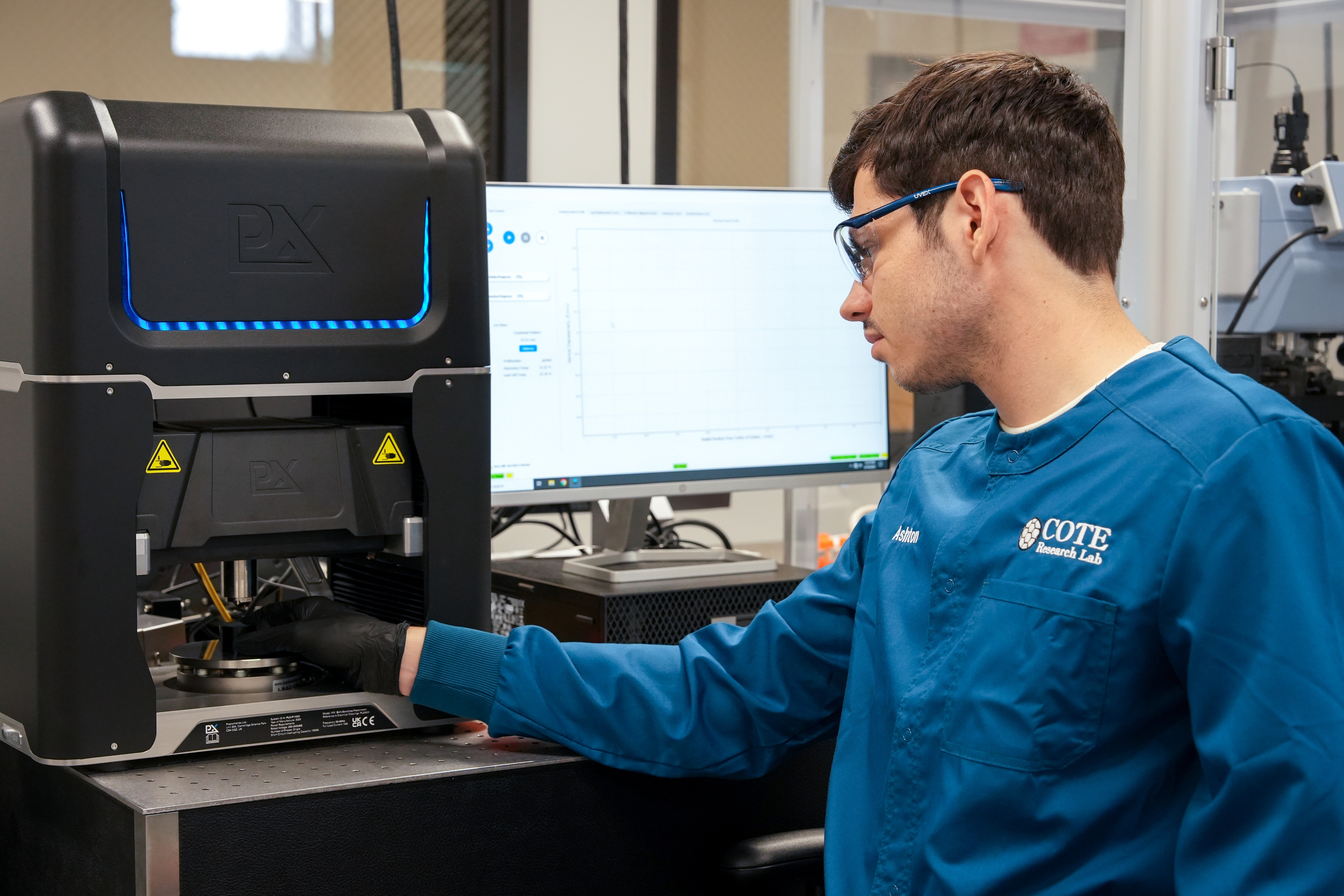
Accelerating R&D with the PLX-Benchtop
WPI’s journey began with the adoption of the PLX-Benchtop system in 2021 to support early-stage materials and process development. At that stage, they needed high-throughput testing and to quickly refine print parameters and evaluate new alloys – often working with small sample volumes. Conventional tensile testing was slowing things down.
By integrating the PLX-Benchtop into their workflow, WPI was able to get key mechanical property data from small, lightly prepared samples, without the delays or waste associated with machining and destructive testing. This, in turn, guaranteed rapid and efficient characterisation of candidate materials and the optimisation of deposition parameters. The PLX-Benchtop allowed them to:
- Quickly screen a wide range of materials, accelerating the material down-selection process.
- Optimise printing and deposition parameters efficiently, using real mechanical property data to enable precise adjustment of deposition parameters.
- Minimise material waste, which is crucially important for small batches of potentially expensive or experimental feedstocks.
- Rapidly generate comprehensive data sets, providing a strong foundation for their material and process decisions.
This first step set the foundation for a more agile R&D workflow. With the PLX-Benchtop, researchers at WPI could save valuable time and resources while quickly identifying the most promising materials and process parameters.
“With the PLX tech suite, we’re able to generate the data we need faster, with less material, and with greater granularity across printed parts. It’s been a game-changer for our research, and the support from Plastometrex has made every step of adoption seamless.” Prof. Danielle Cote, Associate Professor, Materials Science and Engineering
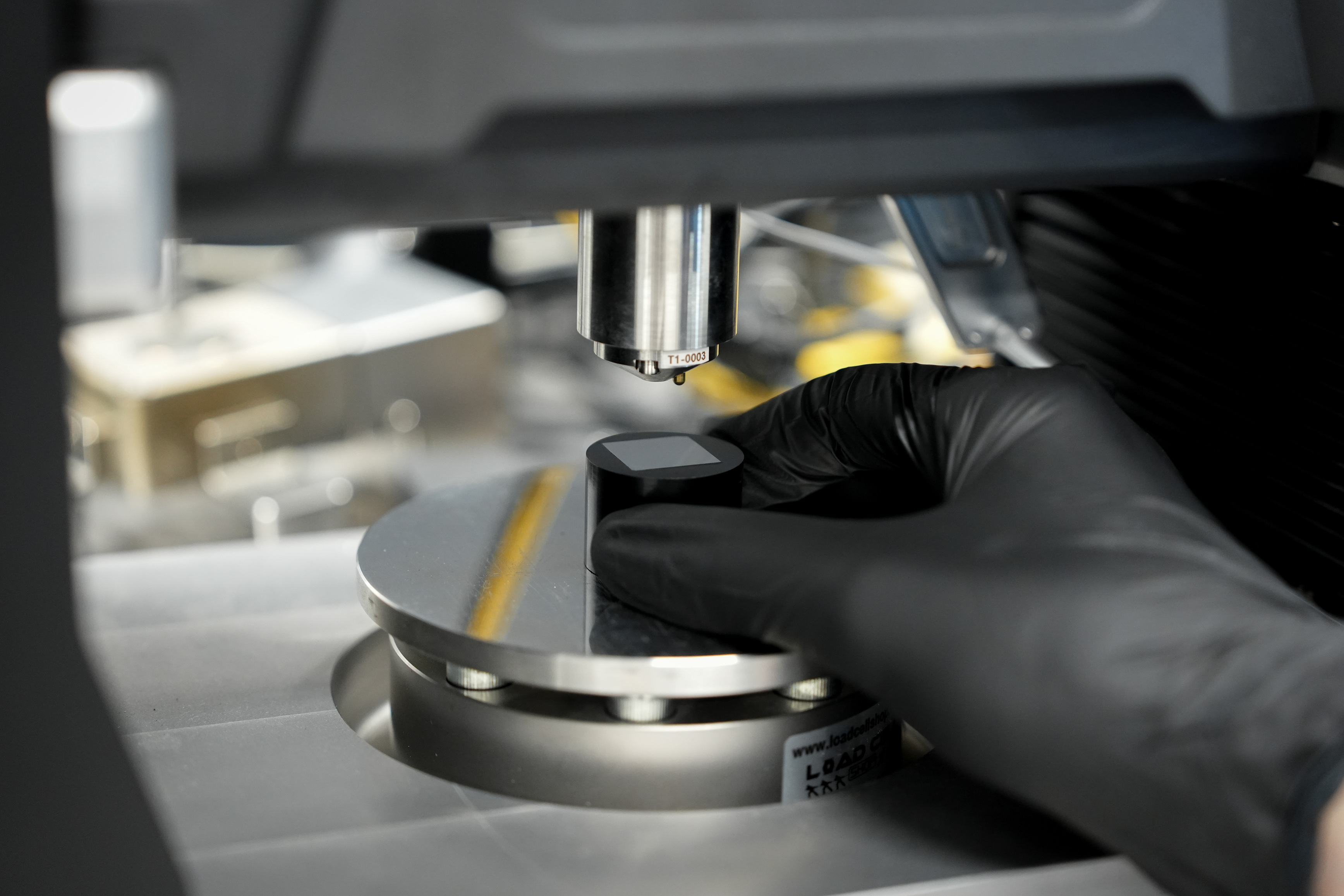
Gathering High-Temperature Insights with the PLX-HotStage
After the successful integration of the PLX-Benchtop into their lab, the team at WPI began looking to expand the role of PIP testing in their operations. Many of the AM components they were developing would be expected to operate under demanding conditions, including elevated temperatures.
To better predict part performance, the Cote Research Lab integrated in 2023 the newly launched PLX-HotStage into its development cycle. This modular attachment to the PLX-Benchtop gave researchers the ability to characterise material properties at temperatures up to 800°C. Because these high-temperature tests can be performed directly on AM components without the need for separate tensile coupons, researchers at WPI were able to extract critical data on part performance that otherwise wouldn’t be available. Using the PLX-HotStage, the team could:
- Assess material performance under realistic operating conditions, providing data on representative in-service performance.
- Optimise processes for high-temperature applications, ensuring optimal performance at elevated temperatures and enhancing component reliability.
- Avoid expensive and time-consuming furnace-based testing with a faster and more cost-effective alternative to traditional high-temperature testing methods.
- Investigate temperature-dependent material behaviour, gaining a deeper understanding of the fundamental mechanisms governing material response at high temperatures.
With these new testing capabilities, the team at WPI can better bridge the gap between R&D and deployment: gathering accurate mechanical property data under real-world conditions that allows for better, faster component optimisation.
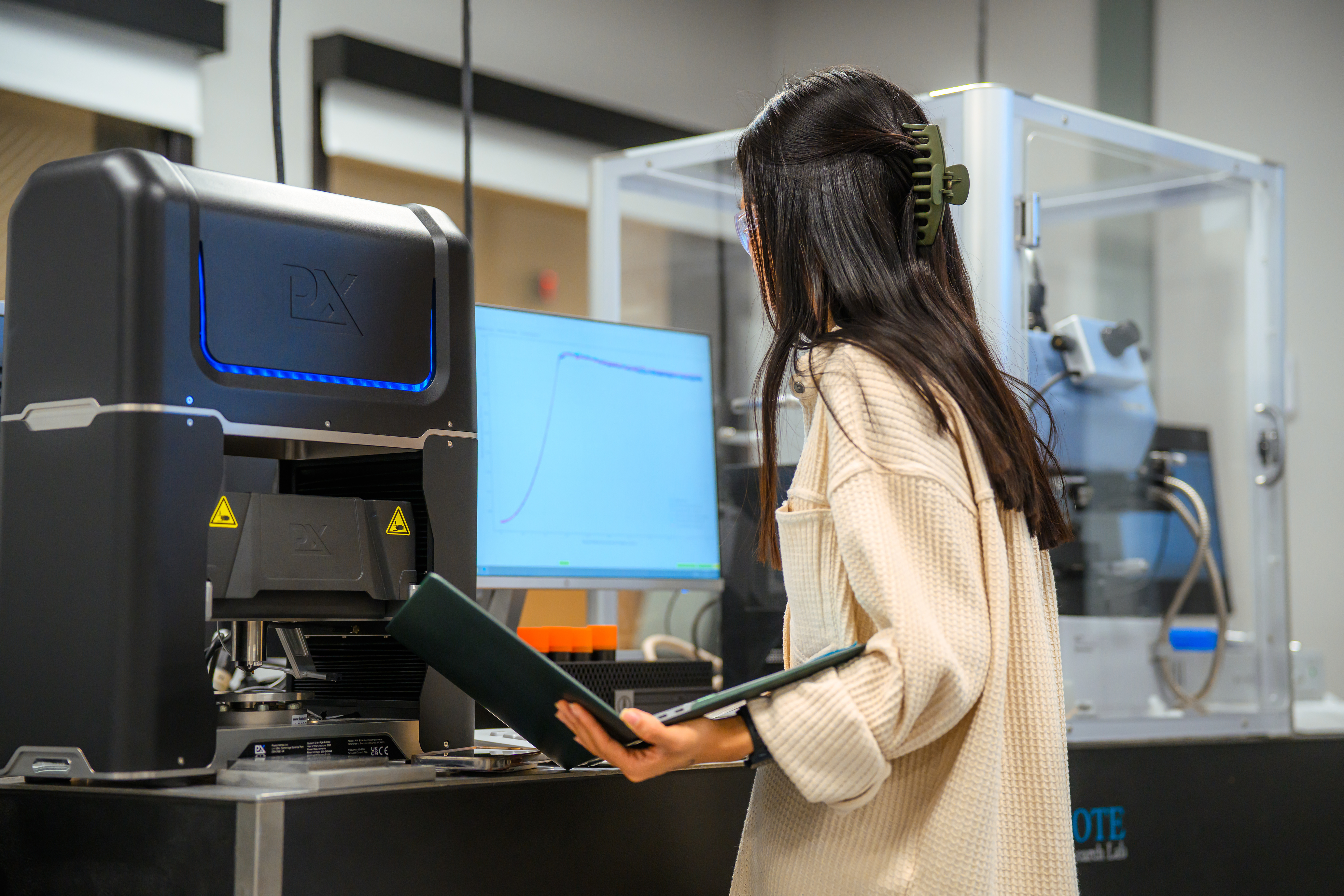
Ensuring Quality and Performance of Prototype Components with PLX-Portable
Seeing the impact of the PLX-Benchtop and PLX-HotStage on their research workflows, WPI recognised an opportunity to expand their PIP testing capabilities even further. With these tools already fully integrated into their material development processes, the team saw the potential to bring the same level of insight to larger, fully-built components.
In 2024, this led to their adoption of the PLX-Portable, a compact testing device originally built for in-field material verification of pipelines. The PLX-Portable allowed WPI to extend its mechanical testing abilities beyond the lab and towards the production floor, providing fast in-field qualification of cold sprayed parts which can be deployed at the point of need. With the PLX-Portable, WPI can:
- Rapidly iterate and optimise mechanical properties for prototype components, providing immediate feedback on the effectiveness of process adjustments.
- Non-destructively validate part performance without the need for destructive testing.
- Enhance quality assurance and quality control (QA/QC), enabling WPI to monitor process stability, detect deviations, and ensure the consistency and reliability of their AM production.
- Generate real-world performance data from actual components in their intended application environment, demonstrating how manufacturing variations could affect in-service performance.
With the full suite of Plastometrex technology at their disposal, the team at WPI can rapidly go from prototype development to full-scale production with confidence in the quality and performance of their AM components.
“Plastometrex’s technology changed the way we think about mechanical testing. It gave us the confidence to move faster, make better decisions, and trust the data at every stage, from lab experiments to real-world builds.” Prof. Danielle Cote, Associate Professor, Materials Science and Engineering
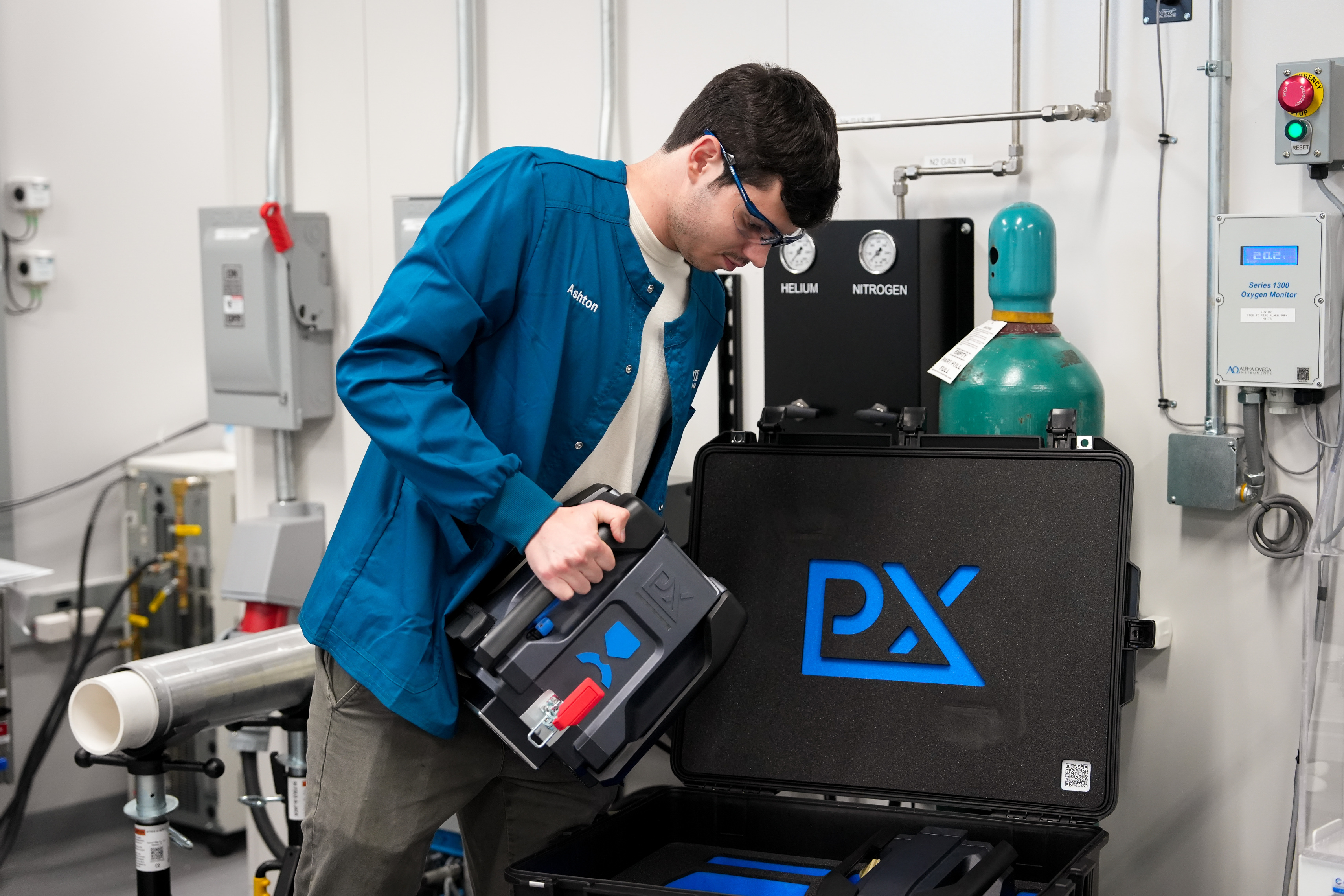
Accelerating Time to Value
Since WPI’s initial adoption of the PLX-Benchtop, Plastometrex’s Applications Engineering and Customer Support teams have worked alongside WPI, helping to ensure the seamless implementation of each system and providing deep, engaged support to keep operations running smoothly. Today, the team at the Cote Research Lab knows that they can rely on the Plastometrex technology and team in equal measure: a collaboration built on a shared commitment to advancing the future of additive manufacturing.
“The support has been fantastic. Anytime we’ve had a question, big or small, someone from Plastometrex is right there with an answer or a practical solution. That kind of backing is rare.” Kyle Tsaknopoulos, Assistant Research Professor
Today, the Cote Research Lab has a fully integrated PLX testing suite - one that enables faster experimentation, smarter decisions, and a more direct path from concept to deployment. And behind it all is a partnership built on shared innovation, trust, and a deep commitment to accelerating the future of additive manufacturing.