Additive manufacturing (AM) is revolutionising industries, offering unprecedented design freedom and material efficiency. However, ensuring the mechanical integrity of 3D-printed components remains a challenge, particularly due to issues such as anisotropy and build inhomogeneity.
At the 2025 Additive Manufacturing Users Group (AMUG) Conference, we showcased how Profilometry-based Indentation Plastometry (PIP) is accelerating AM part qualification. The method can be used to rapidly determine the mechanical properties of a part, without the need to print separate tensile coupons. By giving manufacturers the ability to test directly on printed components, PIP provides deeper insights than conventional methods. As a result, users can quickly and easily optimise build parameters, leading to stronger, more reliable components.
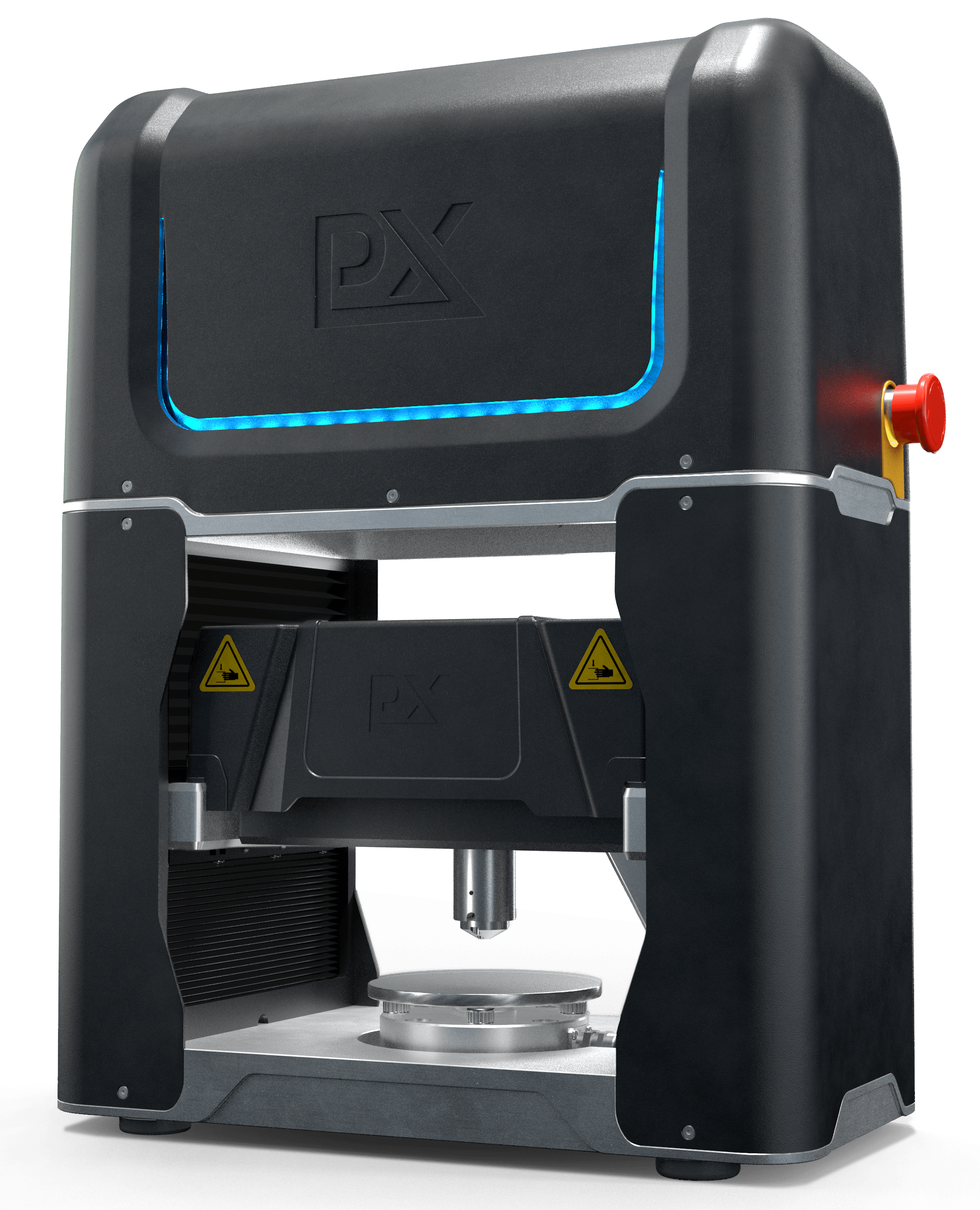
Overcoming Challenges in AM Parameter Optimisation
The ability to accurately assess local mechanical properties is critical for ensuring part performance and process optimisation within AM. PIP allows for efficient, localised mechanical testing without the need for extensive sample preparation. This technique is particularly useful for detecting inhomogeneities, identifying mechanical anisotropy, and evaluating how printing parameters influence material properties.
By offering a rapid and cost-effective alternative to traditional tensile testing, PIP can be implemented much earlier in the parameter development process, enabling manufacturers to optimise build parameters beyond density measurements alone. This was demonstrated in our collaboration with Additive Manufacturing Solutions, where PIP was used to rapidly assess the effects of different process variables on mechanical properties. By identifying trends in mechanical performance early in development, manufacturers can refine print parameters more efficiently, ensuring stronger and more reliable parts while reducing time and cost.
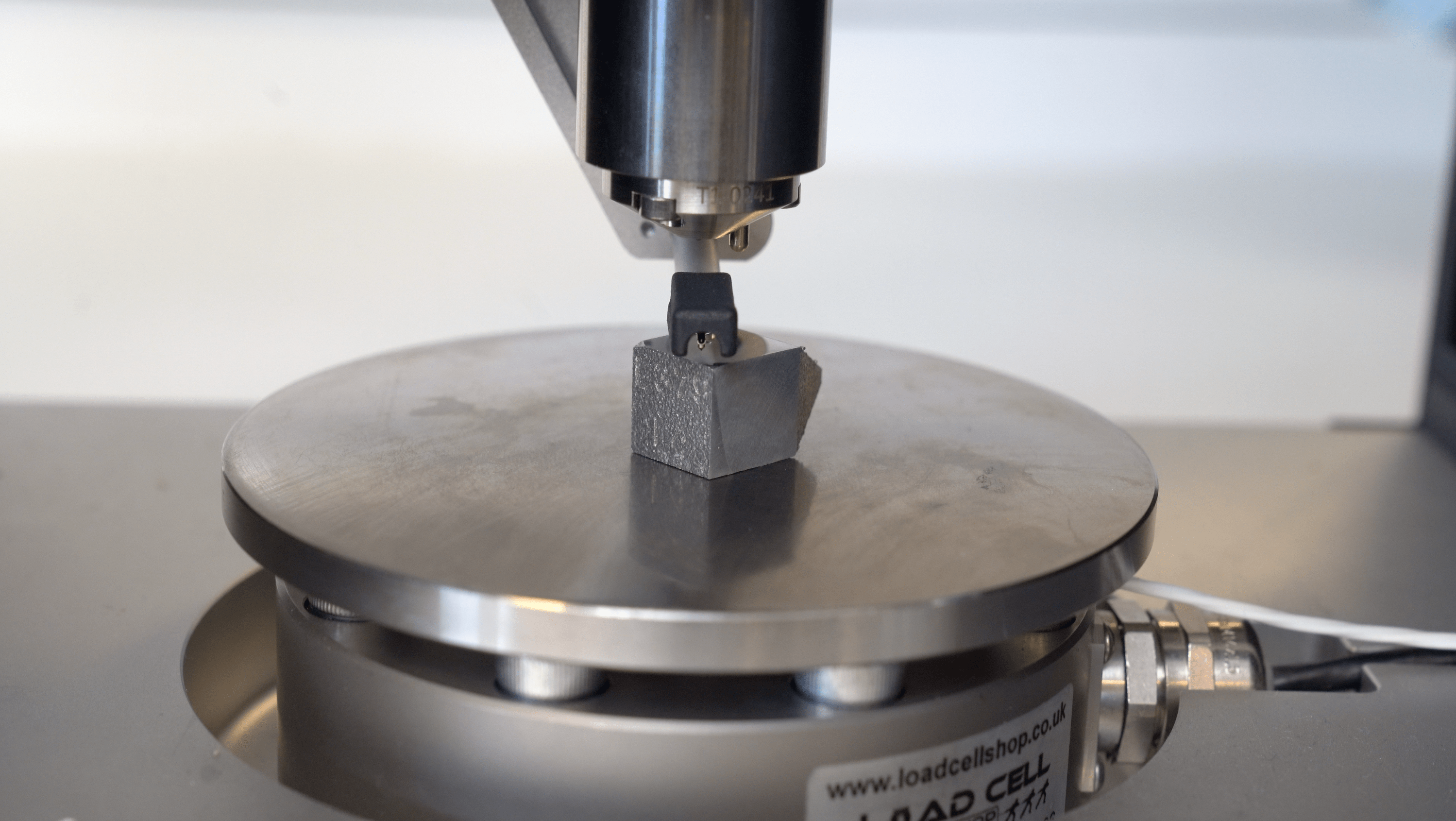
Case Studies: AM Part Quality
At AMUG 2025, we presented multiple case studies demonstrating the effectiveness of PIP across various stages of AM implementation. We explored how the PLX-Benchtop serves as a key characterisation tool throughout various stages of AM development, including through-process testing with Renishaw, anisotropy analysis with NASA, and inhomogeneity detection in final parts with Alloyed.
In our collaborative case study with Renishaw, PIP tests were repeated on E8 tensile coupons throughout different stages of heat treatment and post-processing. By testing on the same coupons throughout processing, we could track the evolution of each tensile coupon’s mechanical properties, providing a clearer understanding of how each processing step influences final part performance.
With NASA, we investigated anisotropy in AM components by performing localised mechanical tests in different orientations. PIP enabled a detailed analysis of directional variations in mechanical properties, highlighting how printing parameters and thermal history contribute to anisotropy.
Our work with Alloyed concentrated on detecting inhomogeneities in final parts and correlating these variations to geometric features. PIP's high spatial resolution made it possible to map mechanical property distributions across complex geometries, providing insights that conventional tensile testing could not capture.
Enhancing AM Process Development with PIP
The ability to rapidly characterise mechanical properties at small scales is critical for improving AM part qualification and process optimisation. By integrating PIP testing into AM workflows, manufacturers gain deeper insights into anisotropy, inhomogeneity, and mechanical performance. This leads to higher-quality parts, more efficient process optimisation, and reduced production costs. PIP is not only accelerating testing but also providing additive manufacturing engineers with a powerful tool for achieving unmatched component performance.
Want to learn more about the PLX-Benchtop? Click here.